What Is The Aluminum Anodizing Process
Updated: 26 Jul 2023
Aluminum anodizing is an electrochemical process that creates a protective oxide layer on the surface of aluminum and its alloys. The anodizing process enhances the metal's corrosion resistance, improves its wear resistance, provides a base for decorative finishes, and can be used as a surface preparation for painting or bonding. Here's a general overview of the aluminum anodizing process:
Surface Preparation: The first step involves cleaning the aluminum surface to remove any dirt, oil, or other contaminants. This is crucial to ensure a uniform anodized layer.
Acid Etching (Optional): In some cases, the aluminum may undergo an acid etching process to smoothen the surface and remove any impurities. This step is usually skipped for certain alloys or applications.
Anodizing Bath: The cleaned aluminum is immersed in an electrolytic bath containing an acidic electrolyte solution, typically based on sulfuric acid. The aluminum acts as the anode in the electrolytic cell, and a cathode is also present.
Electrolysis: An electric current is passed through the electrolyte solution, causing oxygen ions to be released at the anode (aluminum surface). The oxygen ions react with the aluminum atoms on the surface, forming aluminum oxide (Al2O3).
Anodic Oxide Formation: The aluminum oxide layer grows on the surface of the aluminum. This layer is porous and adheres tightly to the metal substrate.
Control of Thickness: The thickness of the anodized layer can be controlled by adjusting the time and voltage of the anodizing process. Thicker layers are generally more wear-resistant and suitable for applications requiring greater protection.
Dyeing (Optional): If desired, the anodized aluminum can be colored by immersing it in a dye bath. The porous oxide layer absorbs the dye, resulting in a colored surface. This is often used for decorative purposes.
Sealing: After anodizing and dyeing (if applicable), the aluminum is sealed to close the pores in the anodized layer. This is typically done using hot water or steam, which causes the aluminum oxide to swell and seal the pores, improving corrosion resistance.
Quality Control: The final anodized aluminum product undergoes quality control checks to ensure that the specified thickness, color (if applicable), and other desired properties are achieved.
The specific details of the anodizing process may vary depending on the type of aluminum alloy, the desired outcome, and the application for which the anodized aluminum will be used. Different industries use anodized aluminum for various products, including architectural finishes, automotive parts, consumer electronics, and aerospace components.
Application environment: understand the environment in which the customer's product will be used, and whether anti-corrosion, anti-oxidation, or wear resistance are required.
Appearance requirements: consider the customer's requirements for product appearance, such as gloss, color, texture, etc.
Coating thickness: Determine the coating thickness required to ensure that the product's functional requirements are met.
Cost budget: Different anodizing types and coloring options may have different costs, which need to be selected according to the customer's budget.
Production Process: Consider the customer's production process and requirements to ensure that the selected anodizing and coloring options are compatible.
Aluminum parts that have been anodized are resistant to wear, do not rust over time, and are suitable for use in architectural finishes like doors, window profiles, LED light strip profiles, and aluminum edge trim for tiles.
If you're looking for a way to make your aluminum parts more durable, corrosion-resistant, and aesthetically pleasing, aluminum anodizing may be the solution you need. This multi-step finishing process not only strengthens the surface layer of the metal, but can also alter its color and texture to create a more attractive design. To explore your options for aluminum anodizing, parts finishing, or other extrusion services, get in touch with Shenghai Aluminum today or request a quote online.
Surface Preparation: The first step involves cleaning the aluminum surface to remove any dirt, oil, or other contaminants. This is crucial to ensure a uniform anodized layer.
Acid Etching (Optional): In some cases, the aluminum may undergo an acid etching process to smoothen the surface and remove any impurities. This step is usually skipped for certain alloys or applications.
Anodizing Bath: The cleaned aluminum is immersed in an electrolytic bath containing an acidic electrolyte solution, typically based on sulfuric acid. The aluminum acts as the anode in the electrolytic cell, and a cathode is also present.
Electrolysis: An electric current is passed through the electrolyte solution, causing oxygen ions to be released at the anode (aluminum surface). The oxygen ions react with the aluminum atoms on the surface, forming aluminum oxide (Al2O3).
Anodic Oxide Formation: The aluminum oxide layer grows on the surface of the aluminum. This layer is porous and adheres tightly to the metal substrate.
Control of Thickness: The thickness of the anodized layer can be controlled by adjusting the time and voltage of the anodizing process. Thicker layers are generally more wear-resistant and suitable for applications requiring greater protection.
Dyeing (Optional): If desired, the anodized aluminum can be colored by immersing it in a dye bath. The porous oxide layer absorbs the dye, resulting in a colored surface. This is often used for decorative purposes.
Sealing: After anodizing and dyeing (if applicable), the aluminum is sealed to close the pores in the anodized layer. This is typically done using hot water or steam, which causes the aluminum oxide to swell and seal the pores, improving corrosion resistance.
Quality Control: The final anodized aluminum product undergoes quality control checks to ensure that the specified thickness, color (if applicable), and other desired properties are achieved.
The specific details of the anodizing process may vary depending on the type of aluminum alloy, the desired outcome, and the application for which the anodized aluminum will be used. Different industries use anodized aluminum for various products, including architectural finishes, automotive parts, consumer electronics, and aerospace components.
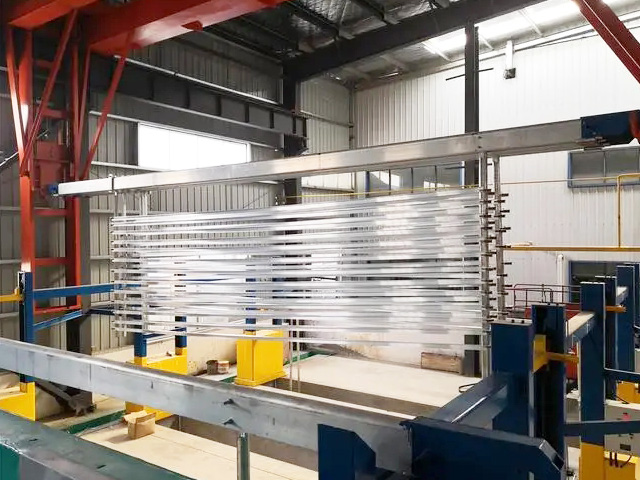
Choose Aluminum Profile Anodizing
Here are some factors to consider when helping customers choose the correct anodizing type and coloring option:Application environment: understand the environment in which the customer's product will be used, and whether anti-corrosion, anti-oxidation, or wear resistance are required.
Appearance requirements: consider the customer's requirements for product appearance, such as gloss, color, texture, etc.
Coating thickness: Determine the coating thickness required to ensure that the product's functional requirements are met.
Cost budget: Different anodizing types and coloring options may have different costs, which need to be selected according to the customer's budget.
Production Process: Consider the customer's production process and requirements to ensure that the selected anodizing and coloring options are compatible.
Aluminum parts that have been anodized are resistant to wear, do not rust over time, and are suitable for use in architectural finishes like doors, window profiles, LED light strip profiles, and aluminum edge trim for tiles.
If you're looking for a way to make your aluminum parts more durable, corrosion-resistant, and aesthetically pleasing, aluminum anodizing may be the solution you need. This multi-step finishing process not only strengthens the surface layer of the metal, but can also alter its color and texture to create a more attractive design. To explore your options for aluminum anodizing, parts finishing, or other extrusion services, get in touch with Shenghai Aluminum today or request a quote online.