Why Aluminum Alloy Anodizing
Updated: 26 Aug 2024
To overcome the defects of aluminum alloy surface hardness, wear resistance, etc., expand the scope of application, and extend the service life, aluminum alloy anodizing manufacturers have become indispensable in aluminum alloy use in surface treatment technology. Anodizing technology is currently widely used and successful.
Hard anodizing uses a DC power supply or a DC and AC superposition power supply. There are many types of solutions, and sulfuric acid hard anodizing is the most common. When using sulfuric acid hard anodizing, various factors that affect the oxide film layer should be considered.
1. Concentration of sulfuric acid oxidation treatment: 200-250 g/L is often used, and the relative density of the bath (at room temperature) is 1.12-1.15.
2. Water: Water is the main component of hard anodizing treatment. Generally, distilled or cold-boiled water is used instead of tap water because tap water contains chloride ions. When Cl—>1%, the parts will corrode during the oxidation process, and white spots will appear.
3. Temperature of oxidation treatment: Temperature is one of the important factors affecting the quality of the oxide film. Strictly controlling the temperature will make the oxide film thicker, the hardness will increase, and it will be smooth and dense.
4. Current density: Current is also one of the important factors affecting the quality of the oxide film. It has a great relationship with the generation rate and organization of the oxide film. When the current density is too low, the generation rate of the oxide film is slow and the processing time increases; on the contrary, when it is too high, the solution and the electrode will overheat due to the Joule effect. The dissolution rate of the oxide film increases, the hardness decreases, and the surface becomes rough, loose and powdery.
5. Initial voltage and processing time: The initial voltage and time of hard anodizing also have a great influence on the quality of the oxide film. If the initial voltage is too large, the current will increase, the Joule heat and the generation heat will increase sharply, and the dissolution rate will increase sharply, and the oxide film will be soft, dull, powdery and not wear-resistant. For the oxidation treatment time, the thickness of the oxide film generally increases with the extension of the oxidation treatment time, but after a certain period, if the applied voltage is not increased, the oxide film will not actually increase. If the time continues to be extended, the oxide film will have low hardness, loose and powdery. On the contrary, if the oxidation treatment time is longer, the oxide film will be thin and not wear-resistant.
6. Stirring of the oxidation treatment solution: The stirring speed is related to the generation rate of the oxide film (the quality of the oxide film).
Sulfuric acid anodizing
Sulfuric acid direct current anodizing is the most widely used anodizing method for aluminum. Its anodized film is colorless and transparent and can be subjected to various coloring treatments. It has good sealing performance and can be used as a corrosion-resistant protective layer. It is low in cost and easy to make to obtain a thicker oxide film to meet various performance requirements.
Butyric acid anodizing
The butyric acid anodizing process depends on the type of component, the alloy composition to be anodized, and the main purpose of anodizing. The chromic acid film is thinner, about 0.5-1.25μm. However, it has quite good corrosion resistance and protection, which can be due to the presence of chromate in it. The color of the oxide film ranges from grayish white to dark gray, and it is not easy to dye; it is softer and less resistant than the sulfuric acid anodized film; the porosity of the film is lower, and it can be used without sealing. The chromic acid method is suitable for parts with small dimensional tolerances and high surface finish, and is also suitable for cast aluminum alloys with large porosity (total alloying elements not more than 1.5% and copper content not more than 59). It is especially suitable for the protection of complex parts or assemblies that do not easily discharge residual electrolytes in the structure, so it is widely used in aircraft manufacturing and machinery manufacturing.
Hard anodizing
Hard anodizing is also carried out in sulfuric acid electrolytes (sometimes appropriately adjusted), and the only difference is the operating temperature and current density. Hard anodizing produces a much thicker anodic oxide film than general sulfuric acid anodizing in a given time. Hard anodizing uses 10-159 sulfuric acid electrolytes, and sometimes additives are added. The operating temperature is The current density at 0-10℃ is 2-3.6Adm. Increasing the temperature forms an anodic oxide film with low hardness and high porosity, thereby reducing the limited film thickness and wear resistance. Excessive operating temperature causes the film to dissolve and even burn the workpiece. The advantages of pulsed direct current in hard anodizing have been relatively certain.
In general, the purpose of anodizing aluminum alloys is to improve their wear resistance and corrosion resistance. When aluminum alloys are in extreme gas environments, in order to prevent corrosion and wear of aluminum alloys, aluminum profile manufacturers usually anodize aluminum to form a thin oxide layer. Anodizing can also be dyed in a variety of colors to meet customer needs. Shenghai Aluminum is a professional aluminum extrusion and deep processing integrated profile factory. If you are looking for a trustworthy aluminum profile manufacturer, you can contact our sales team immediately. We provide you with the best anodized aluminum solutions.
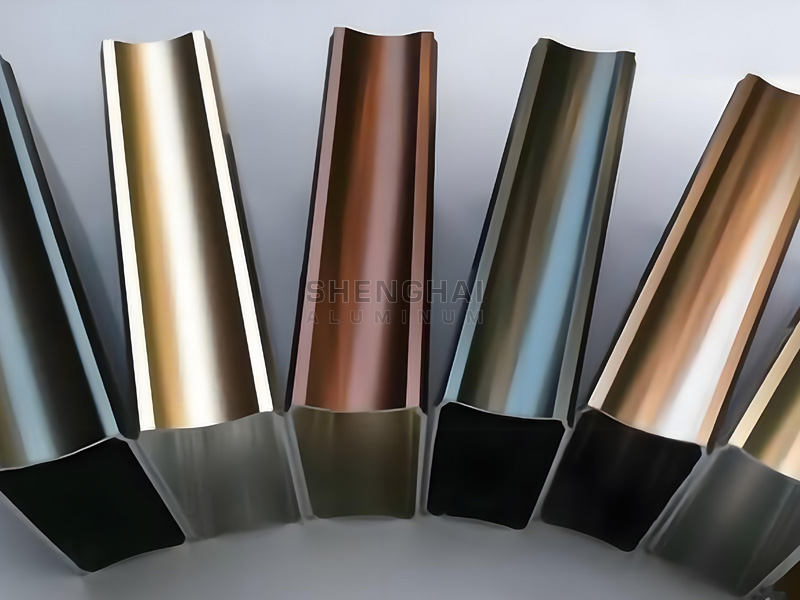
How does aluminum alloy anodizing work
The process of placing aluminum or aluminum alloy products as anodes in electrolyte solutions and using electrolysis to form an aluminum oxide film on their surfaces is called anodizing of aluminum and aluminum alloys. The cathode in the device is a material with high chemical stability in the electrolytic solution, such as lead, stainless steel, aluminum, etc. The principle of aluminum anodizing is the principle of water electrolysis. When current passes through, hydrogen is released at the cathode; at the anode, the oxygen precipitated is not only molecular oxygen but also atomic oxygen (O) and ionic, usually expressed as molecular oxygen in the reaction. Aluminum, as the oxygen, oxidizes the anode precipitated thereon to form an anhydrous aluminum oxide film. The generated oxygen does not all react with aluminum, and part of it is precipitated in the form of gas.Hard anodizing uses a DC power supply or a DC and AC superposition power supply. There are many types of solutions, and sulfuric acid hard anodizing is the most common. When using sulfuric acid hard anodizing, various factors that affect the oxide film layer should be considered.
1. Concentration of sulfuric acid oxidation treatment: 200-250 g/L is often used, and the relative density of the bath (at room temperature) is 1.12-1.15.
2. Water: Water is the main component of hard anodizing treatment. Generally, distilled or cold-boiled water is used instead of tap water because tap water contains chloride ions. When Cl—>1%, the parts will corrode during the oxidation process, and white spots will appear.
3. Temperature of oxidation treatment: Temperature is one of the important factors affecting the quality of the oxide film. Strictly controlling the temperature will make the oxide film thicker, the hardness will increase, and it will be smooth and dense.
4. Current density: Current is also one of the important factors affecting the quality of the oxide film. It has a great relationship with the generation rate and organization of the oxide film. When the current density is too low, the generation rate of the oxide film is slow and the processing time increases; on the contrary, when it is too high, the solution and the electrode will overheat due to the Joule effect. The dissolution rate of the oxide film increases, the hardness decreases, and the surface becomes rough, loose and powdery.
5. Initial voltage and processing time: The initial voltage and time of hard anodizing also have a great influence on the quality of the oxide film. If the initial voltage is too large, the current will increase, the Joule heat and the generation heat will increase sharply, and the dissolution rate will increase sharply, and the oxide film will be soft, dull, powdery and not wear-resistant. For the oxidation treatment time, the thickness of the oxide film generally increases with the extension of the oxidation treatment time, but after a certain period, if the applied voltage is not increased, the oxide film will not actually increase. If the time continues to be extended, the oxide film will have low hardness, loose and powdery. On the contrary, if the oxidation treatment time is longer, the oxide film will be thin and not wear-resistant.
6. Stirring of the oxidation treatment solution: The stirring speed is related to the generation rate of the oxide film (the quality of the oxide film).
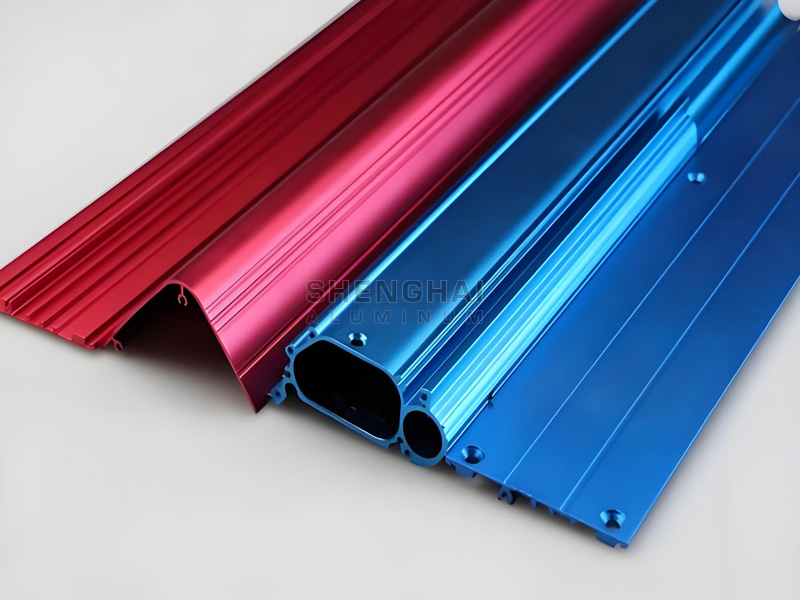
What types of aluminum anodizing processes are there
Anodizing aluminum is a common surface treatment method. There are three main types of anodizing processes commonly used by aluminum profile manufacturers:Sulfuric acid anodizing
Sulfuric acid direct current anodizing is the most widely used anodizing method for aluminum. Its anodized film is colorless and transparent and can be subjected to various coloring treatments. It has good sealing performance and can be used as a corrosion-resistant protective layer. It is low in cost and easy to make to obtain a thicker oxide film to meet various performance requirements.
Butyric acid anodizing
The butyric acid anodizing process depends on the type of component, the alloy composition to be anodized, and the main purpose of anodizing. The chromic acid film is thinner, about 0.5-1.25μm. However, it has quite good corrosion resistance and protection, which can be due to the presence of chromate in it. The color of the oxide film ranges from grayish white to dark gray, and it is not easy to dye; it is softer and less resistant than the sulfuric acid anodized film; the porosity of the film is lower, and it can be used without sealing. The chromic acid method is suitable for parts with small dimensional tolerances and high surface finish, and is also suitable for cast aluminum alloys with large porosity (total alloying elements not more than 1.5% and copper content not more than 59). It is especially suitable for the protection of complex parts or assemblies that do not easily discharge residual electrolytes in the structure, so it is widely used in aircraft manufacturing and machinery manufacturing.
Hard anodizing
Hard anodizing is also carried out in sulfuric acid electrolytes (sometimes appropriately adjusted), and the only difference is the operating temperature and current density. Hard anodizing produces a much thicker anodic oxide film than general sulfuric acid anodizing in a given time. Hard anodizing uses 10-159 sulfuric acid electrolytes, and sometimes additives are added. The operating temperature is The current density at 0-10℃ is 2-3.6Adm. Increasing the temperature forms an anodic oxide film with low hardness and high porosity, thereby reducing the limited film thickness and wear resistance. Excessive operating temperature causes the film to dissolve and even burn the workpiece. The advantages of pulsed direct current in hard anodizing have been relatively certain.
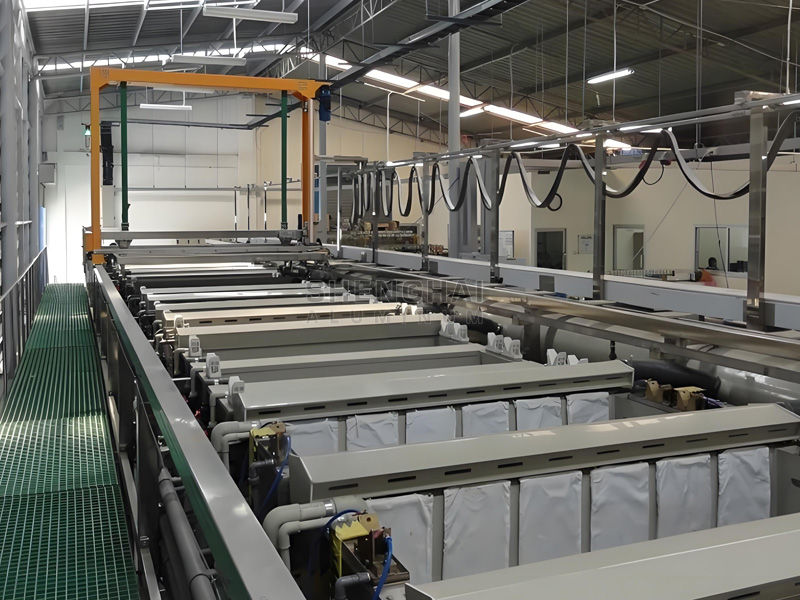